DualFill Pro DFS-9000 Series
2-Head Inline Net Weight Filler & Crimp Sealer with DFS Smart Cart
±0.05% Accuracy ? 40 Pails/H ? ATEX/FDA Certified ? Industry 4.0 Integration
Technical Specifications
Parameter | DFS-9100 (Standard) | DFS-9200X (ATEX) | DFS-9300H (High-Visc) |
---|
Capacity Range | 1-20L (±0.05%) | 1-20L (±0.08%) | 1-20L (±0.06%) |
Throughput | 40 Containers/H | 36 Containers/H | 32 Containers/H |
Accuracy | ±0.05% Gravimetric | ±0.08% | ±0.06% |
Viscosity Range | 50-500,000 cP | 100-300,000 cP | 5,000-1,000,000 cP |
Container Types | Gallons ? 5-20L Pails ? Jerrycans | Same + Safety Cans | Same + Cubitainers |
Filling Technology | Dual Coriolis Mass Flow Meters | ATEX Gear Pumps | Heated Screw Auger |
Crimp Force | 800-5000N (±1%) | 1000-6000N (±1.5%) | 1200-7000N (±1.2%) |
DFS Cart Capacity | 200L (4×50L Totes) | Same + ATEX Pressurization | Same + Heated Jacket |
Material Tracking | RFID/NFC Auto-ID | Same | Same |
Changeover Time | <90s (Tool-Free) | <100s | <85s |
Power | 480V/60Hz, 8.5kW | 24VDC Ex ia | 480V/60Hz, 11kW |
Certifications | NTEP/OIML R117 | ATEX Zone 2 | FDA 21 CFR 177.2600 |
Footprint (L×W) | 3.5m×1.8m | 3.8m×2.0m | 3.6m×1.9m |
Core Innovations
1. DFS SmartCart? System
SmartCart Features:
Function | Technology | Performance |
---|
Collision Avoidance | LiDAR + Ultrasonic Sensors | 0.5m Detection Range |
Auto-Replenishment | Weight Monitoring + Predictive Alert | <2% Stockout Risk |
Safety System | SIL-2 Emergency Brake | 0.3s Response Time |
2. SyncFill? Dual-Head Control
Component | Innovation | Precision |
---|
Cross-Channel Calibration | Real-Time Density Compensation | ±0.02% Head Variance |
Adaptive Crimping | AI-Force Profiling | 99.99% Seal Integrity |
Residual Control | Vacuum Suction + Capillary Break | <0.05ml Residual |
Industry-Specific Engineering
Chemicals & Solvents
Feature | Certification |
---|
ATEX Zone 1 | Pressurized DFS Cart |
VOC Containment | Activated Carbon Filtration |
Corrosion Resistance | Hastelloy C276 Flow Path |
Food & Pharma
GMP Compliance:
Component | Standard |
---|
316L EP Surfaces | FDA 21 CFR 177.2600 |
Cleanability | EHEDG EL Class I |
Batch Traceability:
Industrial Lubricants
Challenge | Solution |
---|
High-Viscosity | 80°C Heated Path + Screw Auger |
Settling | DFS Cart Agitation System |
Static Risk | Ionized Air Curtain (10? ions/cm3) |
Smart Control Ecosystem
**10" HMI with DFS-OS?**
IIoT Features:
Predictive Maintenance:
Component | Alert Threshold |
---|
Crimp Head Wear | Force Deviation >5% |
Seal Degradation | Friction >10N |
Quality Assurance:
Parameter | Precision |
---|
Fill Weight | ±0.05% (NTEP Class III) |
Seal Integrity | Helium Test <10?? mbar·L/s |
Lid Alignment | ±0.3mm Vision Inspection |
Operational Workflow
1. Pail Loading → 2. DFS Cart Auto-Docking →
3. Net Weight Taring (±0.01%) → 4. Dual-Head Filling (±0.05%) →
5. Vacuum Nozzle Retraction → 6. AI-Guided Crimping (800-5000N) →
7. 100% Seal Verification → 8. DFS Cart Auto-Replenishment
Cycle Time: 90 seconds/pail
Certifications
? ATEX 2014/34/EU Zone 1 (DFS-9200X)
? FDA 21 CFR 177.2600
? NTEP Certificate 19-032
? OIML R117 Class 0.5
? ISO 9001:2015
DFS SmartCart Specifications
Parameter | DFS-9100 |
---|
Capacity | 200L (4×50L Totes) |
Weight | 320kg (Empty) |
Height Adjustment | 800-1200mm Auto-Leveling |
Safety System | SIL-2 Brake + Lid Sensor |
Battery | 10h Operation/LiFePO? |
Connectivity | OPC UA/5G/Wi-Fi 6 |
Performance Validation
Dow Chemical Case Study:
*"After 6 months using DFS-9100:
Output: 22 → 40 pails/hour (+82%)
Material Loss: 0.8% → 0.03% ($380k/year saved)
Seal Failures: 1.2% → 0.01%
ROI: 5.8 months"*
Why Choose DFS-9000?
Industry 4.0 Integration:
? DFS SmartCart Advantages:
- Real-Time Material Tracking (RFID/NFC)
- Collision Avoidance (LiDAR + AI Vision)
- Auto-Height Docking (±1mm)
? Precision Engineering:
| **Component** | **Performance**|
|----------------------|------------------------|
| Dual Coriolis Meters | ±0.02% Synchronization |
| Servo Crimp Head | 5000N Force ±1% |
| Load Cells | 0.002% Repeatability|
? Safety Architecture:
1. ATEX Pressurized Enclosure
2. Gas Detection System (1% LEL)
3. SIL-2 Emergency Stop
APPLICABLE BARREL TYPE
COMPANY PROFILE
Shanghai Guangzhi Automation Equipment Co., Ltd. is a production and trading company specializing in the weighing industry. We are located in Shanghai, China's economic city, with convenient transportation and export ports all over the world. We cooperate with state-owned factories and international companies, and the quality is guaranteed.
We mainly focus on providing customers with weighing solutions, from commercial scales to industrial weighing machines. Such as pneumatic valve bag packaging machine, dry mix mortar bag packaging machine, cement packaging machine, natural stone powder packaging machine, flour powder packaging machine, wheat packaging machine, potato starch packaging machine, air packaging machine, granule bag packaging machine, grain packaging machine, fertilizer bag packaging machine, lubricant filling machine, 200 kg drum filling machine, 216L drum filling machine, 208L drum filling machine, ton barrel filling machine, IBC barrel filling machine, jumbo bag packaging machine, ton bag packaging machine, 30L pail filling machine, 50L pail asphalt filling machine, ATEX barrel filling machine, explosion-proof filling machine, etc.
Live Shooting
Support customization, low price, no middlemen, factory direct sales, large quantity and more favorable. Product quality assurance, simple operation and durability. We have professional customer service to consult and provide technical guidance at any time.
Our office and workshop
Consulting-Design-Procurement-Processing-Production-Installation-Debugging-Training-Maintenance
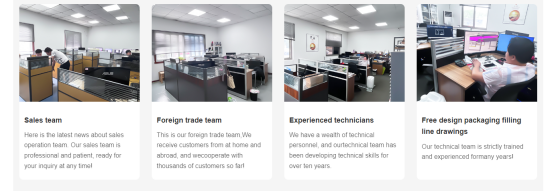
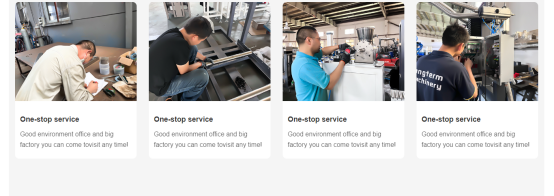
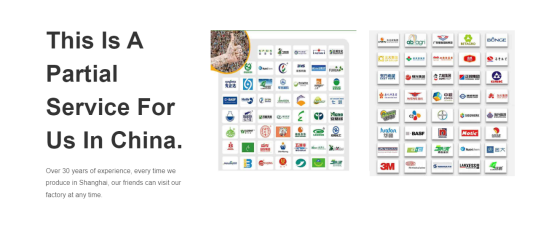
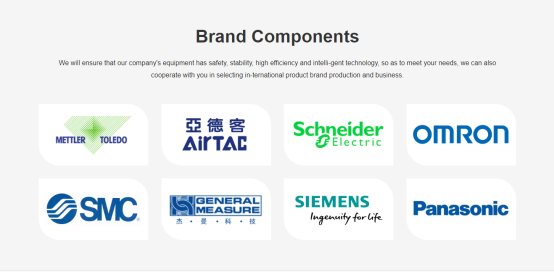
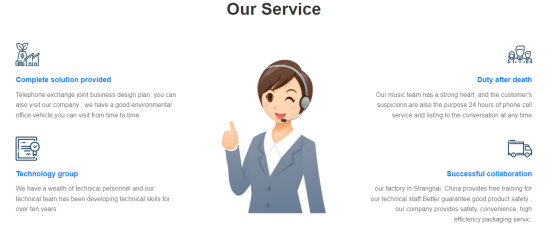
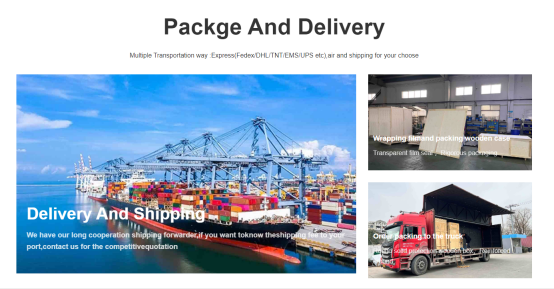
